An Introduction to Composite Materials
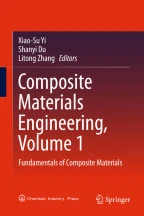
A composite is a material with two or more distinct constituents or phases that have different physical or chemical properties, which are constructed into a complex architecture at micro-, meso- or macro-scale levels. The development and application of single materials like metals, ceramics and polymers has led to the combination of such materials to form synthetic composites.
This is a preview of subscription content, log in via an institution to check access.
Access this chapter
Subscribe and save
Springer+ Basic
€32.70 /Month
- Get 10 units per month
- Download Article/Chapter or eBook
- 1 Unit = 1 Article or 1 Chapter
- Cancel anytime
Buy Now
Price includes VAT (France)
eBook EUR 277.13 Price includes VAT (France)
Softcover Book EUR 348.14 Price includes VAT (France)
Hardcover Book EUR 348.14 Price includes VAT (France)
Tax calculation will be finalised at checkout
Purchases are for personal use only
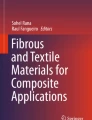
Introduction to Composite Materials
Chapter © 2016
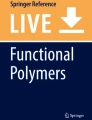
Composites and Nanocomposites
Chapter © 2019

Composites and Nanocomposites
Chapter © 2019
References
- Zou ZW (1999) Structure and properties of composite materials (trans: Wu R-J). The Science Press, Beijing (in Chinese) Google Scholar
- Yi XS (1991) An introduction to laminated adhering composites. Jilin Science and Technology Press (in Chinese) Google Scholar
- Schijve J, van Lipzig H, van Gestel G, Hoeymakers A (1979) Fatigue properties of adhesive bonded laminated sheet material of aluminum alloys. Eng Fract Mech 12:561–579 Google Scholar
- Schijve J (1994) Fatigue of aircraft materials and structure. Fatigue 16:21–32 Google Scholar
- Marissen R (1980) Fatigue properties of aramid reinforced aluminum laminates. Thesis, Delft University of Technology, Netherlands Google Scholar
- Marissen R (1988) Fatigue crack growth in ARALL (Aramid reinforced aluminum laminates)—A hybrid aluminum-aramid composite material: Crack growth mechanisms and quantitative predictions of the crack growth rates. Report DFVLR-FB-88-56, Dissertation (Dr.-Ing), DFVLR, Cologne, Germany Google Scholar
- Roebroeks GHJJ, Intvelt JC (1986) Mechanistic aspects of fatigue crack growth in ARALL. Report VTH-LR-502. Department of Aerospace Engineering, Delft University of Technology, Netherlands Google Scholar
- Roebroeks GHJJ (1987) Constant amplitude fatigue of ARALL-2 laminates. Report LR-539. Dept. of Aerospace Engineering, Delft University of Technology, Netherlands Google Scholar
- Roebroeks GHJJ (1986) Observation of cyclic delamination in ARALL under fatigue loading. Report VTH-LR-496, Department of Aerospace Engineering, Delft University of Technology, Netherlands Google Scholar
- Chen D (1987) Some aspects of test frequency influence on the fatigue behavior of ARALL, Report LR-549. Department of Aerospace Engineering, Delft University of Technology, Netherlands Google Scholar
- Yi XS (1991) An introduction to laminated adhering composites. Jilin Press of Science and Technology, Changchun (in Chinese) Google Scholar
- Yi XS (2004) Challenges and innovations of advanced composite materials. Aeronaut Manuf Technol 7:24–30 (in Chinese) Google Scholar
- Anon (1996) New materials for next-generation commercial transport. Committee on New Materials for Advanced Civil Aircraft, National Materials Advisory Board, Aeronautical Materials Advisory Board, Aeronautical and Space Engineering Board, Commission on Engineering and Technical Systems, National Research Council, NMAB-476, The National Academic Press of America, Washington DC Google Scholar
- Yi XS (2003) The general ex-situ technique to prepare the toughness phase and high toughness composite. National Defense Patent, 200310102017.0 (in Chinese) Google Scholar
- An X, Ji S, Tang B et al (2002) Toughness improvement of carbon laminates by periodic interleaving thin thermoplastic films. J Mater Sci Lett 21:1763–1765 (in Chinese) ArticleGoogle Scholar
- Yi XS, An X, Tang B et al (2002) Ex-situ formation of periodic interlayer structure to significantly improve the impact damage resistance of carbon laminates. Adv Eng Mater 83(14):3117–3122 Google Scholar
- Xu YH (2003) The study of RTM resin and ex-situ RTM technology. Thesis, Beijing Institute of Aeronautical Materials (in Chinese) Google Scholar
- Tang BM, Yi XS (2003) A general technique for preparation of toughness phase and high toughening composite material by ex-situ processing. 200310102017.0 (in Chinese) Google Scholar
- F-22 Raptor Materials and Processes (2004) www.globalsecurity.org/military/systems/aircraft/f-22-mp.html
- RTM-Worx (2004) (Simulation of resin transfer molding and vacuum infusion). www.polyworx.com
- Yi XS (2003) The infusion processing method by ex-situ resin film, 03105536.2 (in Chinese) Google Scholar
- Yi XS (2001) The method to improve the toughness of composite laminate. Defense Patent, 01 100981.0 (in Chinese) Google Scholar
- Yi XS (2001) One method to improve the toughness of intra-layer laminates. Patent No. 01 1 00981.0, China (in Chinese) Google Scholar
- Li Y, Yi X, Tang B (2004) Experimental study on PEK-C modified epoxies and the carbon fiber composites for aerospace application. Chin J Aeronaut 13(4):242–250 (in Chinese) Google Scholar
- An XF (2004) The study on the laminated-toughened polymeric matrix laminates. Thesis, Zhejiang University (in Chinese) Google Scholar
- Yi XS, An X (2004) Effect of interleaf sequence on impact damage and residual strength in a graphite/epoxy laminate. J Mater Sci Lett 39:3253–3255 Google Scholar
- Anon (1999) Prepreg remains strong. High Performance Composites, Jan/Feb Google Scholar
- Anon (1999) Pragmatism prevails in aerospace industry. Reinforced Plastics, Jan Google Scholar
- Anon (2004) Composite aircraft structures, International Symposium on Manufacturing Technology for Composite Aircraft Structures. In: Proceedings of ISCM 2004. Braunschweig Google Scholar
- http://www.lockheedmartin.com/us/products/f22.html (2008)
- http://blog.frponline.com.cn/dutingting/article_1925.html (2008)
- Wu GZ, Asai S, Sumita M (1999) A self-assembled electric conductive network in short carbon fiber filled poly(methyl methacrylate) composites with selective adsorption of polyethylene. Macromolecules 32:3534/3536 Google Scholar
- Wu GZ, Miura T, Asai S, Sumita M (1999) A supramolecular organization in vapor-grown carbon fiber polymer blends. Polym Preprints, Japan, 48(11):2905–2906 Google Scholar
- Wu GZ, Miura T, Asai S, Sumita M (1999) A self-assembly electric conductive network in short carbon fiber filled poly(methyl methacrylate) Composite with selective adsorption of polyethylene. Macromolecules (32):3534–3536 Google Scholar
- Yi XS (2004) Function principle of filled conductive polymer composites. National Defense Industry Press, p 161 (in Chinese) Google Scholar
- Oberlin A, Endo M, Koyama T (1976) Cryst J Growth, (32):335 Google Scholar
- Endo M, Takeuchi K, Kobori K, Takahashi K, Kroto HW, Sarkar A (1995) Carbon 33:873 Google Scholar
- Wu GZ. Miura T, Asai S, Sumita M (2001) Carbon black-loading induced phase fluctuations in PVDF/PMMA miscible blends: dynamic percolation measurements. Polymer 42:3271–3279 Google Scholar
- Li D (2003) The Research on the directionally grown carbon nanotubes composites. Thesis, Tsinghua University (in Chinese) Google Scholar
- Yi XS (2004) Study on energy absorption behavior of composite tubes and integrated manufacturing of composite structure. J Mater Eng 9:3–6 (in Chinese) Google Scholar
- Farley GL (1993) Relationship between mechanical-property and energy absorption trends for composite tube [R]. NASA TP-3284 Google Scholar
- Chiu CH et al (1993) Effects of braiding parameters on energy absorption capability of triaxially braided composite tubes. J Compos Mater 32(2):1964–1983 Google Scholar
- Thornton PH, Edwards PJ (1982) Energy absorption in composite tubes. J Compos Mater 16:521–545 ArticleGoogle Scholar
- Farley Gary L (1983) Energy absorption of composite materials. J Compos Mater 17:267–279 ArticleGoogle Scholar
- McCarthy MA, Wiggenraad JFM (2001) Numerical investigation of a crash test of a composite helicopter subfloor structure. Compos Struct 51:345–359 ArticleGoogle Scholar
- Feng XQ (2001) Effective elastic moduli of polymer-layered silicate nanocomposites. Chin Sci Bull 46(13):1130–1133 (in Chinese) ArticleGoogle Scholar
- Feng XQ (2004) The research on the multi-level structure and property of advanced polymeric composites. The First Report. Beijing, April (in Chinese) Google Scholar
- Wang JJ (2001) The preparation and characterization of PMR PI/AlN composites. Zhejiang University, Hangzhou Shi (in Chinese) Google Scholar
- Hamilton RL et al (1962) Ind Eng Chem Fund 1:187 Google Scholar
- Garrent KW et al (1974) J Phys D: Appl Phys 7:1247 Google Scholar
- Benvensite Y (1987) Appl J Phys 61:2840 Google Scholar
- Hasselman DHP et al (1987) J Comp Mater 21:508 Google Scholar
- Powell BP et al (1980) J Am Ceram Soc 63:581 Google Scholar
- Every AG et al (1992) Acta Metall Mater 40:123 Google Scholar
- Hasselman DHP et al (1992) J Am Ceram Soc 75:3137 Google Scholar
- Davis LC et al (1995) J Appl Phys 77(10):4954 Google Scholar
- Lipton R (1996) Appl J Phys 80:5583 Google Scholar
- Lipton R (1998) Comp J Mater 32(14):1322 Google Scholar
- Yi XS (2004) Function principle of filled conductive polymer composites. National Defense Industry Press, Beijing, pp 229–231 (in Chinese) Google Scholar
- Wang J, Yi XS (2003) Preparing and the properties of PMR-type polyimide composites with aluminum nitride. J Appl Polym Sci 41:1287–1312 Google Scholar
Acknowledgements
The content and examples in this chapter are important for engineering applications and are currently issues in composite research and development. All of these projects were kindly supported by the Fundamental Research Program (National 973 Program), High-Tech Plan (National 863 Plan), National Natural Science Foundation, as well as other pre-research programs and National Tackle Key plans. The author thanks these organizations for their aid.
(Translated by Jianmao Tang and Wenming Zhao; reviewed by Zhen Shen.)
Author information
Authors and Affiliations
- Beijing Institute of Aeronautical Materials, Beijing, 100095, China Xiao-Su Yi
- Xiao-Su Yi